Remain-Core Molding
Remain Core Molding technology, which is the combination of blow molding and injection molding, was pioneered by EXCELL.
A traditional metal intake manifold such as aluminum is replaced to plastic by using Remain Core technology. Excell was the first company to mass produce a plastic intake manifold in Japan.
Remain Core Molding Process
The inner core is formed by blow molding with functional parts, such as a flange, being formed by low-pressure injection molding around the blow molded inner core.
The blow molded core has a non-reinforced nylon layer which reduces inner air flow resistance. The mechanical strength is maintained by molding glass fiber reinforced nylon around this inner core.

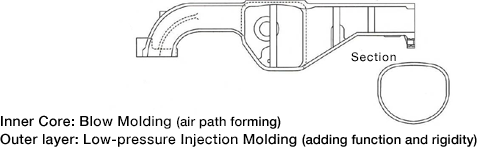
Manufacturing Process of Remain-Core
Blow Molding → Low-pressure Injection Molding → Cutting Work → Assembly Process
As seen above, highly functional products are produced in a very simple manufacturing process.
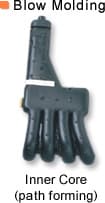
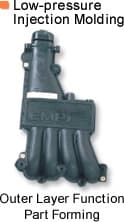
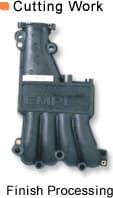
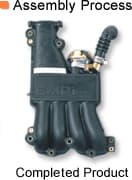
Intake Manifold by Remain-Core Molding Process 01
Weight Reduction, Noise Reduction, Cost Reduction, High Reliability.
30% of weight is reduced by replacing metal parts to plastic.
Remain-Core method is formed with multiple layer of plastics therefore high noise reduction performance is achieved by plastic materials and their combination.
Its sound transmission loss quality is the same as aluminum.
Strength and reliability are high because outer part of Blow Molded product is completely covered by Injection Molding layer.
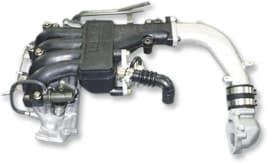
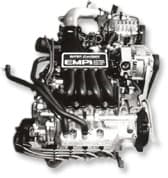

Intake Manifold by Remain-Core Molding Process 02
Design based on commercial production experience with heavy duty engines using super chargers, this application has been adopted for commercial vehicle.
The complicated intake manifold of horizontally opposed engine is replaced to plastic by Remain-Core molding.
![[1] Blow Molded Inner Core/ [2] Injection Molded Part](/assets/images/technology/remain/ph_remain07-en.jpg)
![[3] Fitting harnesses and other parts / [4] Mount onto SUBARU LEGACY](/assets/images/technology/remain/ph_remain08-en.jpg)